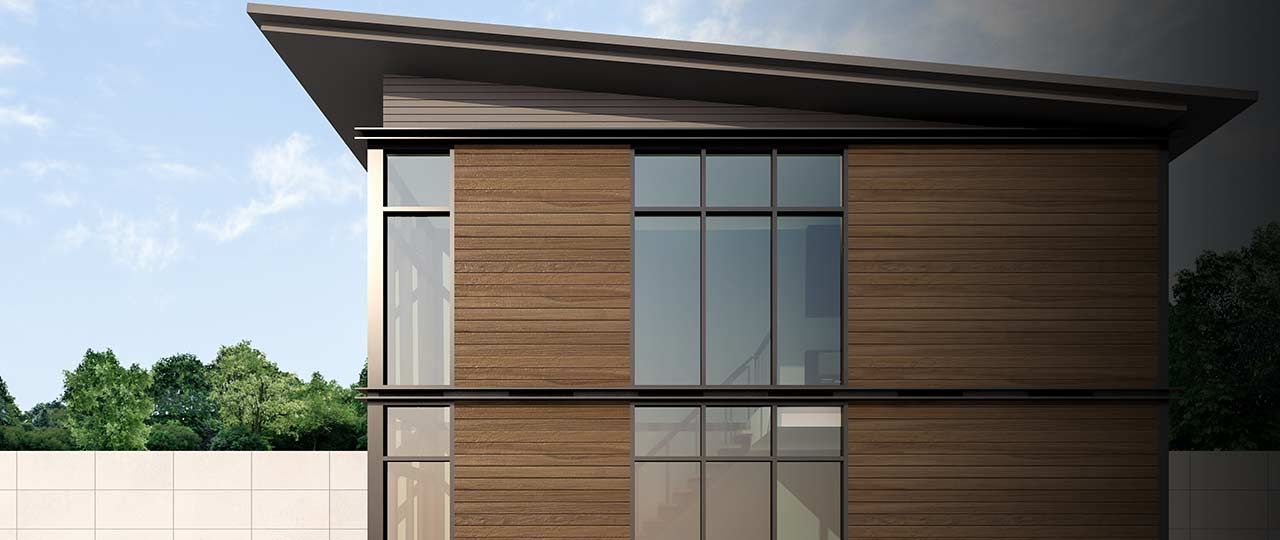
As modular housing begins to take off, we look at some of the challenges of off-site construction and how it could help solve the UK’s housing crisis.
Prefabricated homes are energy efficient and quick to assemble. But in the UK, we’ve lagged behind other countries in adopting this style of construction. We look at the reasons for this reluctance and why many housebuilders are now looking at this new approach to delivering housing.
Getting over the prefab stigma
Modular homes are much less popular in the UK than other countries. Partly, this is down to local building materials: houses in the UK were traditionally built using brick or stone, rather than wood, which lends itself to prefabrication. But another reason that we’ve been slow to adopt new modular home technologies is due to the stigma surrounding prefab housing in this country.
In the post-war years, prefabricated homes were seen as a temporary solution to the housing crisis. Many weren’t intended to last more than a decade, which makes the fact that some are still standing seventy years later, pretty impressive.
By today’s standards, these homes are poorly constructed and leak heat like a holey bucket. Many prefab homes are listed in the Housing Defects Act and, unless they’ve been fully refurbished, it’s almost impossible to get a mortgage on one.
Overcoming this perception is essential to pave the way for a new generation of modular housing. After all, builders are unlikely to commit to a development of homes labelled by mortgage providers as “non-standard”.
The benefits of modular housing
Modern modular housing is a world away from its prefab ancestors. For a start, building standards have moved on a lot since the 1940s when an indoor bathroom was considered a luxury. Today’s modular apartments are energy efficient and built to last.
Many developers also promote eco-friendly credentials, using sustainable materials and construction methods for the build, and incorporating eco features such as solar panels, ground source heating, and rainwater collection systems, making the homes more environmentally friendly and cheaper to run.
The benefits of mass production have been clear since Henry Ford rolled the first Model T off the factory line. Standardising elements of housing design can make production more efficient and allows for greater quality control. And, as the house itself can be built in the factory while the foundations are being laid on site, the whole process can be completed in roughly half the time of a traditional build.
Off-site construction also requires fewer builders, thus addressing one of the construction industry’s most pressing challenges. According to the Royal Institute of Chartered Surveyors, 62 per cent of surveyors reported that a lack of skilled workers was limiting building activity in 2017.
Overcoming the barriers
Offsite construction takes a different approach to housebuilding, both in terms of funding and delivery. More upfront finance is required to invest in the factories and plant required to build homes and this understandably creates a degree of nervousness in the industry, particularly if there is limited political support.
In other European countries, off-site construction is common (84 percent of detached houses in Sweden use prefabricated timber elements) and some European companies see the UK as an untapped market.
The UK construction industry is not blind to this challenge. Berkeley Homes recently announced their aim to build 1,000 modular homes a year out of their new factory in Ebbsfleet, Kent and insurance giant, Legal & General opened their factory in Leeds in 2016, with the aim of producing 4,000 homes a year.
With political support for off-site construction growing, the door of opportunity for UK housebuilders is wide open.
Why modular housing could be the solution to the housing crisis
Affordable housing for first-time buyers is the hot potato of the housing crisis and a huge opportunity for pre-fabricated housing. Currently, most modular homes are apartments. This is partly down to profitability, but also practicality: larger properties are harder to transport on lorries.
Developers such as Pocket Living, which has partnered with the Mayor of London to construct over a thousand modular homes, are taking a new approach to high-density living.
With careful design, Pocket Living aims to create apartments that feel spacious and are affordable to live in, selling for 20 per cent less than the market rate.
The concept can also be applied to family homes. In Manchester, Urban Splash branched out from innovative regeneration schemes to innovative modular design. Their House concept allows customers to design their own two or three storey home, adjusting the layout according to their needs. But while their homes may be quick to build, they aren’t cheap.
The underlying challenges of the housing shortage are much more complex and political than simply finding a quicker way to build. However, factory-built homes address some of the issues, particularly speed of construction and overcoming the shortage of skilled labour. There is clearly an appetite from developers and policy makers to overcome the barriers and introduce more modular housing, and advantages to be passed on to home buyers, so it looks like for many of us, our future homes will be prefabricated!